Precast concrete steps have become an essential component in modern construction, offering durability, versatility, and cost-effectiveness. Whether you're building a commercial property or renovating your home, these steps provide a reliable and aesthetically pleasing solution. In this article, we will explore everything you need to know about precast concrete steps, from their benefits and design considerations to installation and maintenance tips.
The demand for precast concrete steps has grown significantly over the years due to their ability to withstand harsh weather conditions and heavy foot traffic. Architects, builders, and homeowners alike are turning to this material for its strength and longevity. This guide will help you understand why precast concrete steps are a smart choice for any construction project.
In the following sections, we will delve into the advantages of precast concrete steps, how they are manufactured, design options, and important factors to consider before purchasing. Whether you're a professional builder or a DIY enthusiast, this article will provide valuable insights to help you make informed decisions.
Read also:Unveiling The Age Of Kate From Below Deck A Deep Dive
Table of Contents
- Introduction to Precast Concrete Steps
- Benefits of Using Precast Concrete Steps
- How Precast Concrete Steps Are Manufactured
- Design Considerations for Precast Concrete Steps
- Types of Precast Concrete Steps
- Cost Factors for Precast Concrete Steps
- Installation Process for Precast Concrete Steps
- Maintenance Tips for Precast Concrete Steps
- Durability and Longevity of Precast Concrete Steps
- The Future of Precast Concrete Steps
Introduction to Precast Concrete Steps
Precast concrete steps are prefabricated stair systems made from high-strength concrete. They are manufactured off-site in a controlled environment, ensuring consistent quality and reducing the time required for on-site construction. This method offers numerous advantages, including faster installation, reduced labor costs, and enhanced durability.
One of the key reasons for the popularity of precast concrete steps is their ability to withstand extreme weather conditions, such as heavy rain, snow, and temperature fluctuations. Unlike traditional poured-in-place concrete, precast concrete steps are cured in a controlled setting, which minimizes cracking and other structural issues.
Why Choose Precast Concrete Steps?
- Enhanced strength and durability
- Customizable designs to match architectural styles
- Cost-effective and time-saving solution
- Environmentally friendly manufacturing process
Benefits of Using Precast Concrete Steps
Precast concrete steps offer a wide range of benefits that make them an attractive option for both residential and commercial projects. Below, we will explore some of the most significant advantages:
1. Durability and Strength
Precast concrete steps are engineered to withstand heavy foot traffic and harsh environmental conditions. The controlled manufacturing process ensures that the concrete achieves maximum strength before installation, making it less prone to cracking or chipping.
2. Customization Options
One of the standout features of precast concrete steps is the ability to customize their design. From the size and shape to the finish and texture, you can tailor the steps to match the aesthetic of your property. Whether you prefer a sleek modern look or a rustic finish, precast concrete steps can be designed to suit your needs.
3. Cost-Effectiveness
While the upfront cost of precast concrete steps may be slightly higher than traditional poured-in-place concrete, the long-term savings are significant. The reduced labor costs and faster installation time make them a cost-effective option for most projects.
Read also:Unveiling The Life And Legacy Of
How Precast Concrete Steps Are Manufactured
The manufacturing process for precast concrete steps involves several key steps. First, the molds are prepared according to the desired specifications. Reinforcing steel is then added to provide structural integrity, followed by the pouring of high-strength concrete.
Once the concrete is poured, it is allowed to cure in a controlled environment. This ensures that the concrete reaches its full strength before being transported to the job site. The curing process typically takes several days, depending on the specific requirements of the project.
Quality Control in Manufacturing
Quality control is a critical aspect of the manufacturing process. Manufacturers use advanced testing methods to ensure that the concrete meets industry standards for strength, durability, and safety. Regular inspections and testing help to identify and address any potential issues before the steps are shipped to the job site.
Design Considerations for Precast Concrete Steps
When designing precast concrete steps, several factors must be taken into account to ensure safety, functionality, and aesthetics. The rise and run of the steps, as well as the overall layout, must comply with local building codes and regulations.
In addition to functionality, the design of the steps should also complement the surrounding architecture. This can be achieved by selecting the appropriate finish, texture, and color. Popular finishes include exposed aggregate, acid etching, and polishing, each offering a unique look and feel.
Important Design Factors
- Rise and run dimensions
- Compliance with building codes
- Material selection and finishes
- Integration with surrounding landscape
Types of Precast Concrete Steps
There are several types of precast concrete steps available, each suited to different applications. The most common types include:
1. Straight Steps
Straight steps are the simplest and most common type of precast concrete steps. They are ideal for short flights of stairs and can be customized to fit various spaces.
2. L-Shaped Steps
L-shaped steps, also known as quarter-turn steps, are perfect for areas where space is limited. They provide a stylish and functional solution for tight corners.
3. Circular Steps
Circular or spiral steps add a touch of elegance to any property. These steps are often used in high-end residential and commercial projects, providing both form and function.
Cost Factors for Precast Concrete Steps
The cost of precast concrete steps can vary depending on several factors, including size, design, and location. On average, homeowners can expect to pay between $50 and $150 per square foot for precast concrete steps.
Additional costs may include delivery, installation, and finishing touches such as sealants or coatings. It's important to work with a reputable contractor to ensure that all costs are clearly outlined before the project begins.
Factors Affecting Cost
- Size and complexity of the steps
- Type of finish and texture
- Distance from manufacturing plant
- Local labor costs
Installation Process for Precast Concrete Steps
Installing precast concrete steps is a straightforward process when done by experienced professionals. The first step is to prepare the site by leveling the ground and ensuring proper drainage. Once the site is ready, the steps can be lifted into place using cranes or other lifting equipment.
After the steps are positioned, they are secured using anchors or epoxy adhesive. Proper alignment and leveling are critical to ensure safety and functionality. The final step is to apply any finishing touches, such as sealants or anti-slip coatings.
Tips for Successful Installation
- Hire a qualified contractor with experience in precast concrete installation
- Ensure proper site preparation before delivery
- Follow manufacturer guidelines for installation
Maintenance Tips for Precast Concrete Steps
With proper maintenance, precast concrete steps can last for decades. Regular cleaning and inspection can help identify and address any potential issues before they become serious problems. Below are some tips for maintaining your precast concrete steps:
- Regularly clean the steps to remove dirt, debris, and stains
- Apply sealants or coatings to protect against moisture and UV damage
- Inspect for cracks or other signs of wear and repair promptly
Durability and Longevity of Precast Concrete Steps
Precast concrete steps are known for their exceptional durability and longevity. The controlled manufacturing process ensures that the concrete achieves maximum strength and resistance to environmental factors. Proper maintenance can further extend the lifespan of the steps, making them a worthwhile investment for any property.
Studies have shown that precast concrete steps can last up to 50 years or more with minimal maintenance. This makes them an attractive option for properties where long-term durability is a priority.
The Future of Precast Concrete Steps
As technology continues to advance, the future of precast concrete steps looks promising. Innovations in materials and manufacturing processes are expected to further enhance their durability, functionality, and aesthetic appeal. Additionally, the growing focus on sustainability is driving the development of eco-friendly precast concrete solutions.
Manufacturers are also exploring new design possibilities, such as incorporating smart technology into precast concrete steps. This could include features like integrated lighting, sensors, and even solar power generation. These advancements will undoubtedly make precast concrete steps an even more attractive option for future construction projects.
Conclusion
Precast concrete steps offer a durable, versatile, and cost-effective solution for both residential and commercial properties. From their manufacturing process to installation and maintenance, these steps provide numerous benefits that make them a smart choice for any construction project.
We encourage you to explore the possibilities of precast concrete steps for your next project. For more information or to share your thoughts, feel free to leave a comment below. Don't forget to check out our other articles for more insights into construction and design.
Data Source: Concrete Industry Research | OSHA Safety Guidelines
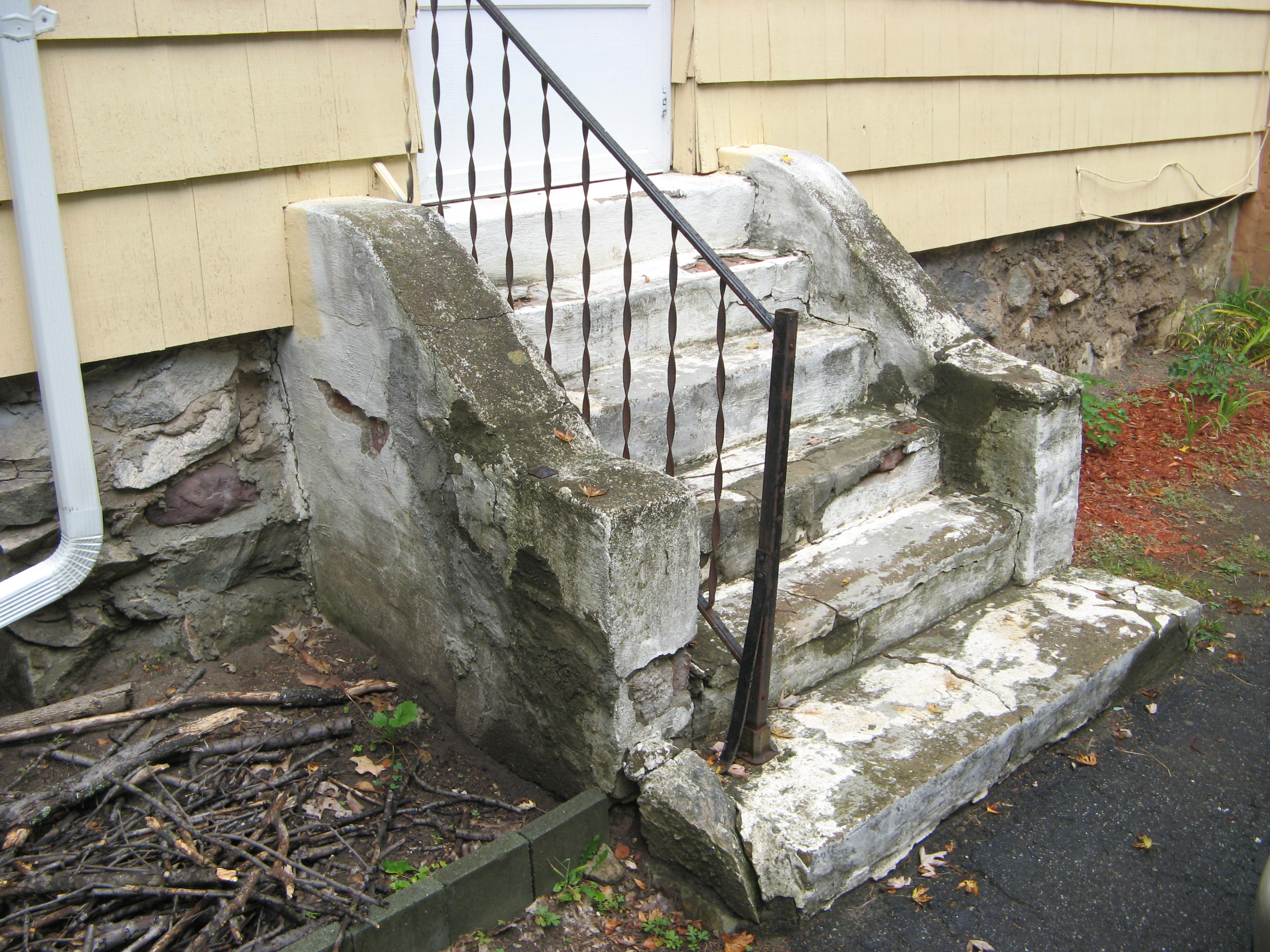
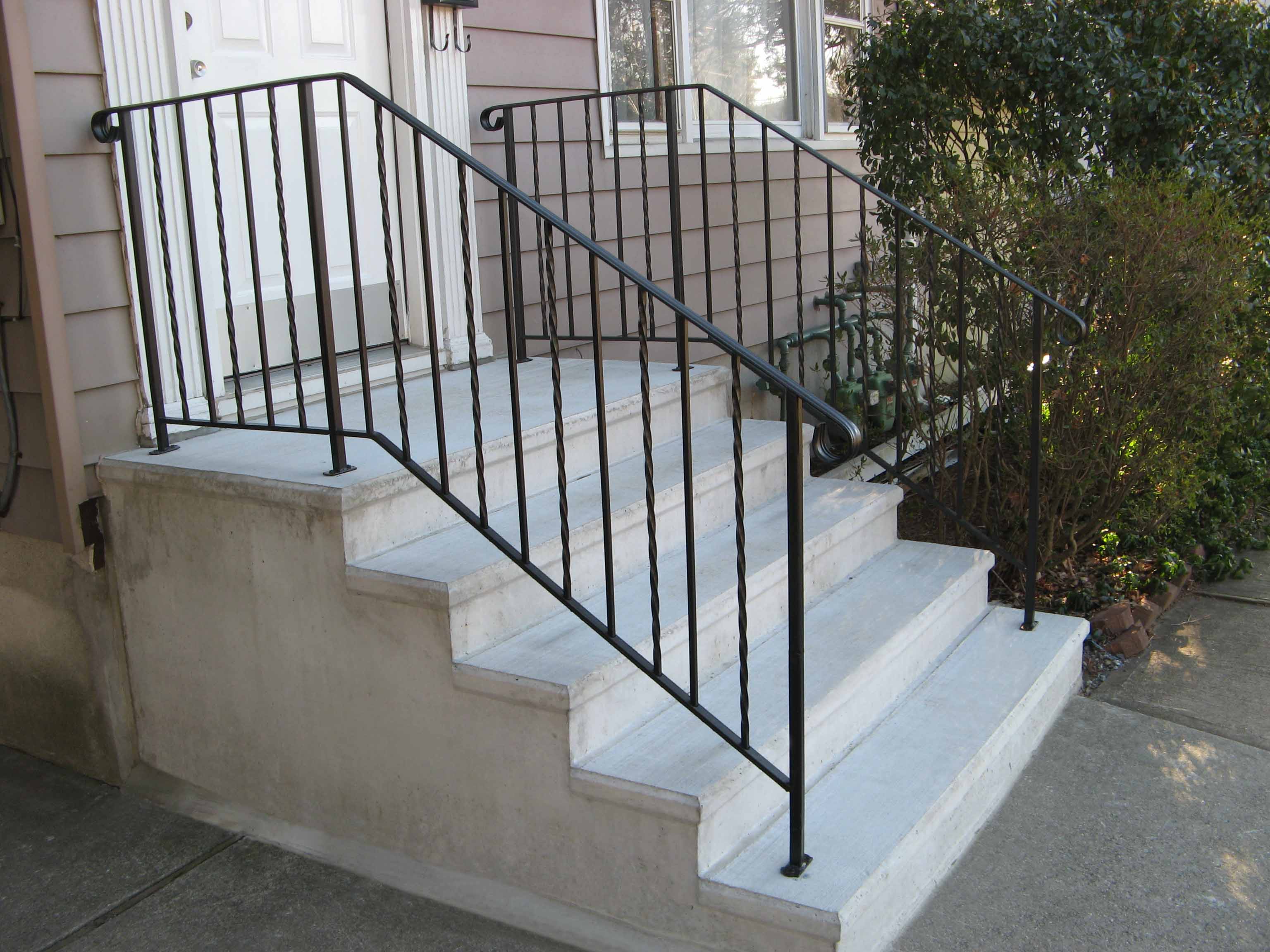
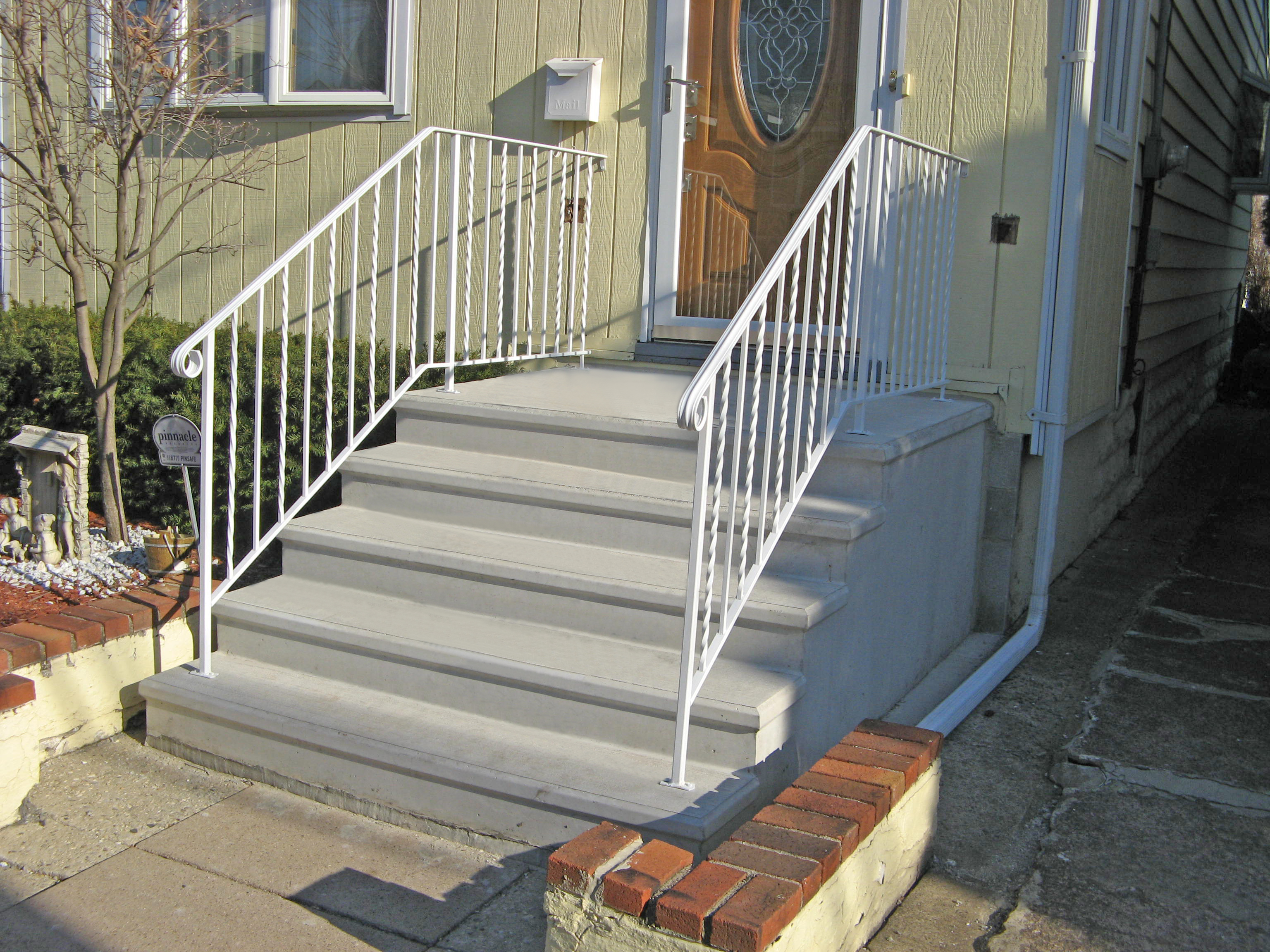
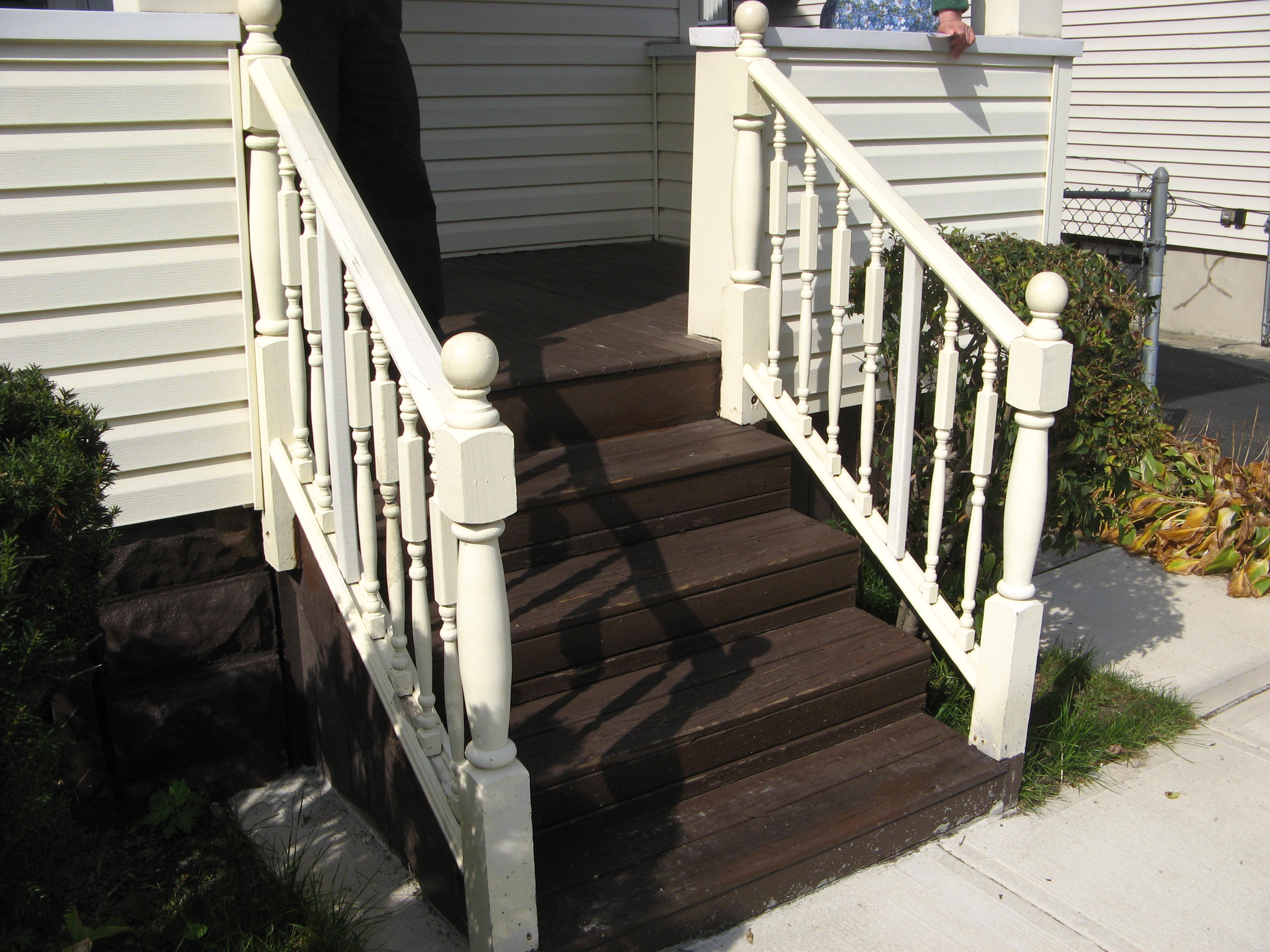